
Resource Dynamics is a carbon management and utilization company that combines innovation and resourcefulness, acting in harmony with nature.
Accumulated waste represents one of the largest untapped energy sources on the planet.
Our eco-friendly carbon conversion system converts high volumes of waste into valuable recycled products.
We re-engineered carbon conversion technology to work on a global scale.
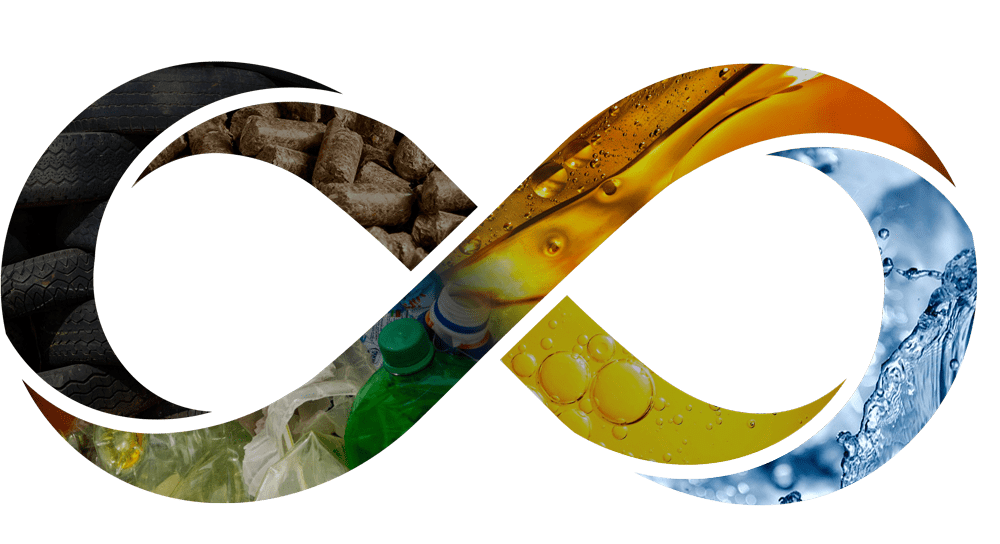
High-Volume
24/7 continuous-feed design; Automated closed-loop system
Scalable
Can stack multiple reactors in one facility
Eco-Friendly
Negligible emissions; Syngas is recycled within the system
Adaptable
Accommodates multiple types of feedstock
Feedstocks Include:
BIOMASS
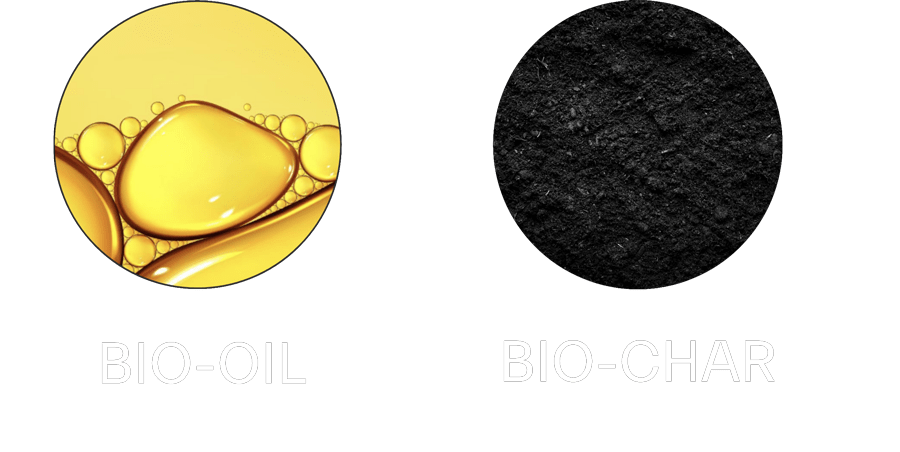
TIRES
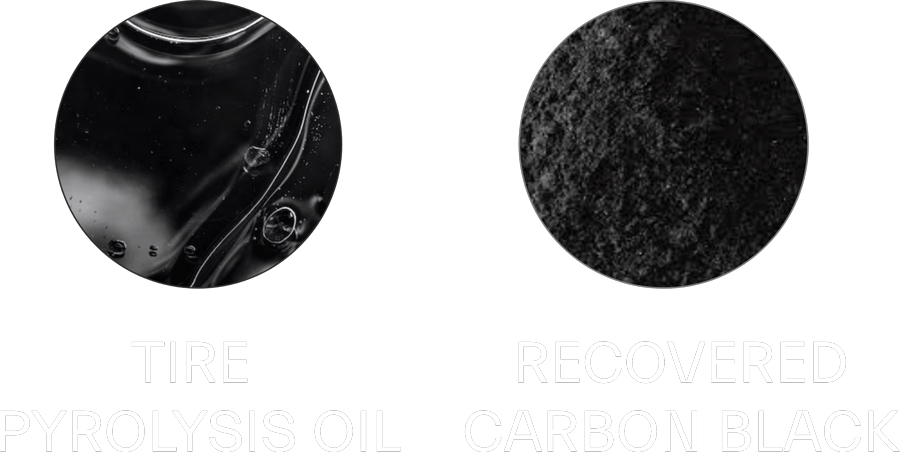
PLASTICS
One carbon conversion reactor can process 15 thousand tons of plastic per year. This can produce liquid feedstock, which can yield about 2.7 million gallons of diesel, is produced.
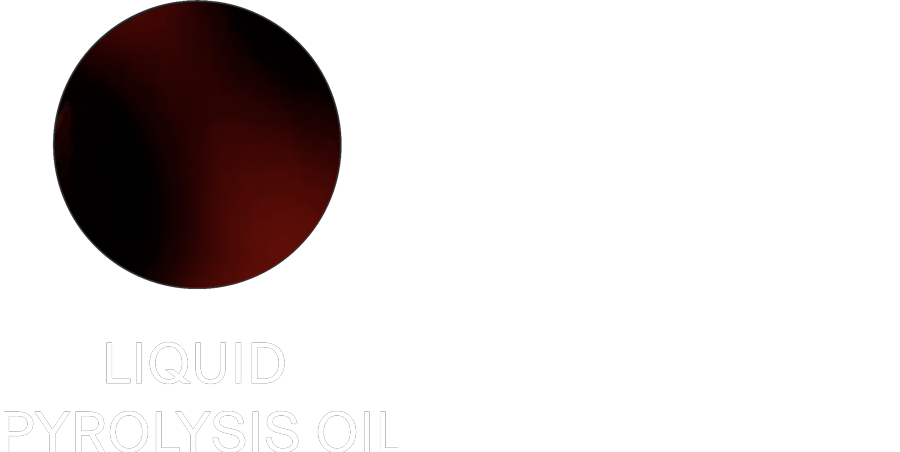
Explore How It Works
Reactor Skid
The Reactor Skid is responsible for breaking down feedstock into gas and solids. Mechanically processed feedstock is fed through a hopper system into one end of the reactor, where the feedstock is exposed to a high-temperature, oxygen-free environment that causes it to be thermally processed into gasses and solids.
Control Center
This is where the entire process is monitored and controlled. Due to changes in feedstock, environmental conditions and output needs, the entire system needs to be monitored to ensure safe processing and maximized commodities.
Condenser & Diesel Skid
Equipment Skid
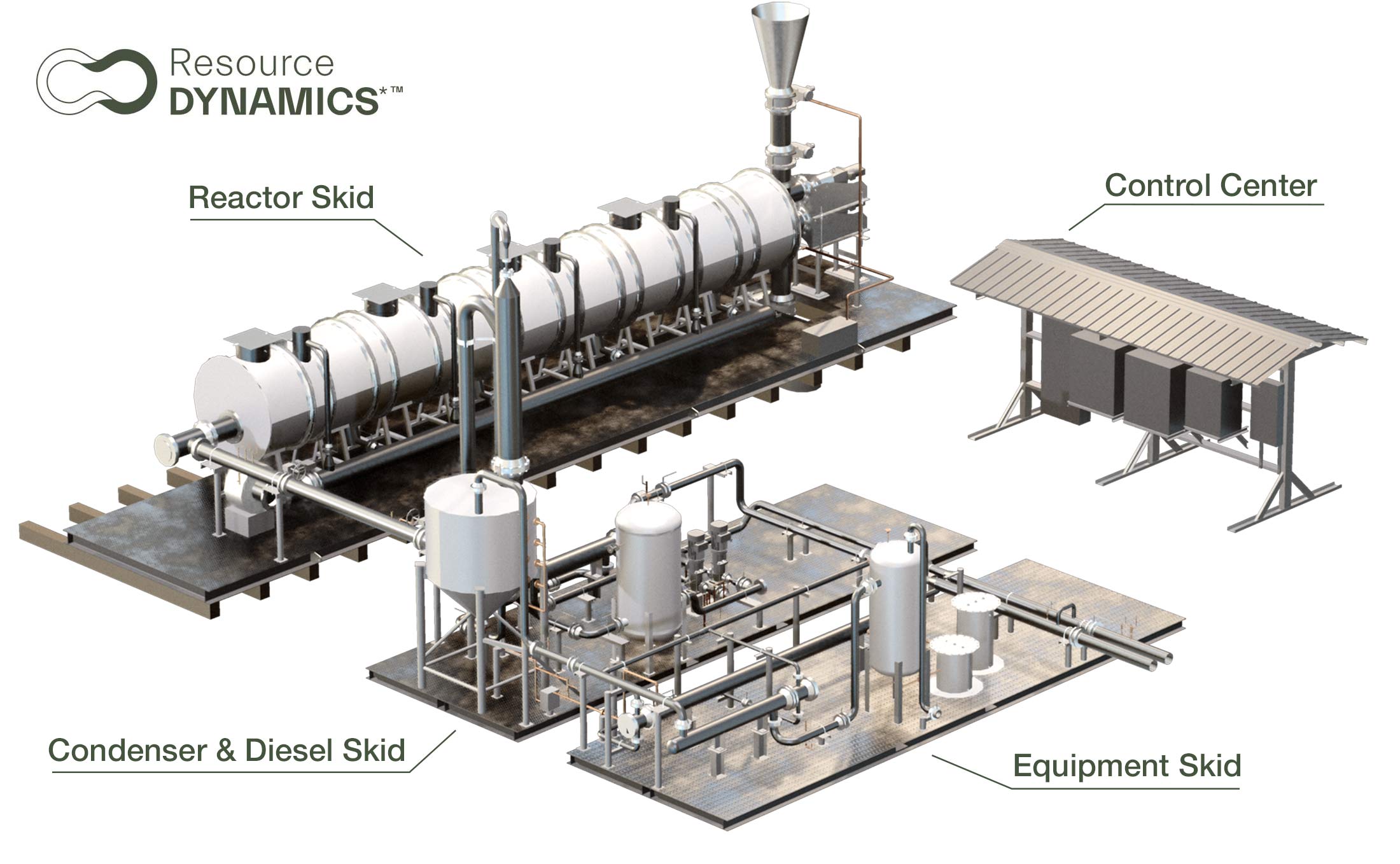

The new global energy system is powered up and ready
Our aim is to liberate the massive energy source in the form of waste on this planet and provide energy independence at the community level and at scale.
Get in touch
Investment Partners
We are scaling quickly!
Reach out to learn more about investment opportunities.
Feedstock Providers
We are looking for waste management, recycling and agricultural partners who want to learn how your feedstock can be converted into marketable commodities.
Industry Insiders
We are collaborators who thrive on connecting with other energy innovators and service providers looking to support far-reaching solutions to our global challenges.
Media Inquiries
We are lining up interviews to share more about Resource Dynamics*™. If your platform or audience would be excited about our work, we’d love to learn more and start a dialogue.
Phone
© 2024 Resource Dynamics*™ A Seraphic Group Company